The Essential Guide to Choosing the Right Nitrogen Regulator for Your Needs
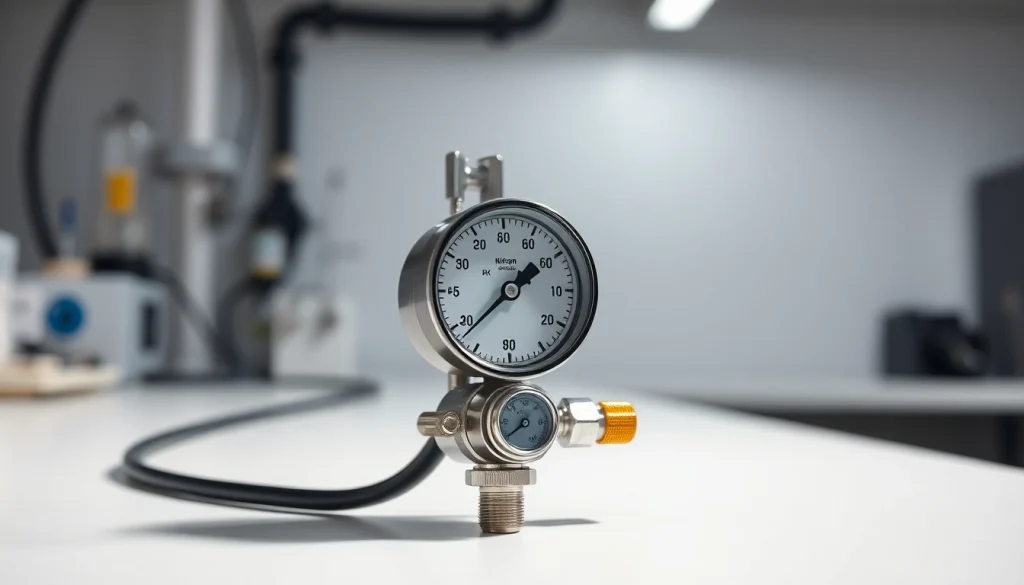
Understanding Nitrogen Regulators
What is a Nitrogen Regulator?
A nitrogen regulator is an essential device used to control the pressure and flow of nitrogen gas from a storage cylinder to various applications. Regulators are critical in ensuring that the pressure of the nitrogen gas is maintained at safe and operational levels. Particularly in industrial settings, precise regulation is necessary to facilitate processes such as refrigeration, HVAC (Heating, Ventilation, and Air Conditioning), and various manufacturing operations.
These regulators convert high-pressure gas from a cylinder, where it is stored at pressures often exceeding 2000 PSI, to the desired lower pressure suited for practical use. The correct utilization of a nitrogen regulator can impact efficiency, safety, and performance in operations where nitrogen is utilized. For more information on choosing a suitable nitrogen regulator, you might explore nitrogen regulator options.
How Nitrogen Regulators Work
Nitrogen regulators operate on the principles of pressure reduction and flow control. At their core, they are designed to balance the pressure in the system with the pressure coming from the source, which is the high-pressure nitrogen cylinder. The key components of a nitrogen regulator include:
- Inlet Valve: It allows the high-pressure gas to enter the regulator.
- Diaphragm: This component responds to the pressure changes and adjusts the flow of gas accordingly.
- Outlet Valve: It controls the release of gas at the desired pressure to the application.
- Gauge: It provides the user with real-time feedback on the pressure levels within the system.
When the nitrogen gas is released from the high-pressure cylinder, it enters the regulator through the inlet. The diaphragm senses changes in the outlet pressure and adjusts the flow accordingly, ensuring that the outlet pressure remains stable whether the demand from the application increases or decreases.
Common Applications for Nitrogen Regulators
Nitrogen regulators are widely utilized in various industries due to the versatile nature of nitrogen gas. Here are some common applications:
- HVAC Systems: Used for pressure testing and purging systems to avoid contamination.
- Refrigeration: Facilitates refrigerant charging and pressure balancing in cooling systems.
- Pneumatic Systems: Controls pneumatic tools and processes wherein nitrogen serves as a working gas.
- Food & Beverage Industry: Applied in kegging systems to dispense beverages while preventing oxidation.
- Manufacturing Processes: Used for inerting, purging, and preserving materials in various production processes.
Choosing the Right Nitrogen Regulator
Key Specifications to Consider
When selecting a nitrogen regulator for a specific application, several crucial specifications must be considered:
- Pressure Range: Ensure the regulator can handle the inlet pressure from the nitrogen source and can deliver it to the desired outlet pressure.
- Connection Type: Evaluate the necessary connection types, such as CGA580 standard, to ensure compatibility with existing systems.
- Flow Rate: Determine the required flow rate for your application to ensure that the regulator can meet the demand under varying conditions.
- Material and Build Quality: Consider materials that resist corrosion and wear, especially in industrial environments.
High Pressure vs. Low Pressure Regulators
Nitrogen regulators can be categorized into high pressure and low pressure based on their intended use:
- High Pressure Regulators: Typically designed for applications requiring pressures above 100 PSI. Often found in industrial setups where high flow is necessary.
- Low Pressure Regulators: Used for applications requiring lower pressures, typically below 100 PSI. Common in food and beverage systems, as well as some HVAC applications.
The choice between high and low pressure regulators will largely depend on the requirements of the specific application. Understanding the operational parameters ensures safety and efficiency.
Understanding Inlet and Outlet Connections
Connection types are critical when it comes to compatibility. Here are key points to consider:
- Inlet Connections: Most nitrogen cylinders utilize a specific connection standard, often CGA580 in the U.S. Verify the inlet type to ensure a secure fit.
- Outlet Connections: Depending on the application, different outlet connection types might be required. Examples include threaded connections for hoses or specific fittings for pressure-sensitive applications.
Ensuring correct and secure connections reduces the risk of leaks and optimizes performance.
Installation and Maintenance of Nitrogen Regulators
Installation Best Practices
Following proper installation procedures is vital for ensuring the safe and effective operation of nitrogen regulators:
- Ensure all components are clean and free from debris before installation.
- Verify that the regulator is compatible with the nitrogen cylinder connection.
- Use Teflon tape or appropriate sealant on threaded connections to prevent leaks.
- Follow manufacturer specifications for assembling the regulator and connecting it to the system.
- Test the system for leaks using soapy water on connections before applying full gas pressure.
Routine Maintenance Tips
Regular maintenance is essential to keep a nitrogen regulator functioning optimally. Some tips include:
- Inspect all connections and components regularly for wear and tear.
- Check gauges for accuracy, recalibrating if necessary.
- Replace seals and O-rings if signs of degradation are evident.
- Ensure the regulator is stored in a clean, dry place when not in use.
Troubleshooting Common Issues
Common issues with nitrogen regulators can usually be diagnosed and resolved without professional help:
- Inconsistent Pressure: This may indicate a faulty gauge or a compromised inner diaphragm. Inspect and replace components as necessary.
- Leaks at Connections: Tightening fittings may resolve minor leaks. Utilize leak detection solutions to identify the source.
- Low Flow Rates: This can often be attributed to blockages or excessive demand exceeding the regulator’s capacity. Review application demands and tank levels.
Safety Considerations with Nitrogen Regulators
Understanding the Risks
While nitrogen is a safe gas, improper handling and use of nitrogen regulators can pose risks such as:
- Pressure Injuries: High-pressure systems can cause physical harm if fittings or hoses fail. Always use protective gear and inspect systems regularly.
- Asphyxiation: Nitrogen is an asphyxiant in confined spaces. Ensure that adequate ventilation is maintained when using nitrogen in enclosed areas.
- Cylinder Hazards: Always handle gas cylinders according to safety standards, securing them to prevent falling and protecting from extremes in temperature.
Safety Equipment and Protocols
For safe operations involving nitrogen regulators, the following safety equipment and protocols should be in place:
- Personal Protective Equipment (PPE): Goggles, gloves, and face shields should be worn while handling nitrogen systems.
- Ventilation Systems: Ensure sufficient airflow in areas where nitrogen gas is being utilized to mitigate risks associated with confined environments.
- Regular Training: Conduct ongoing training and safety drills for personnel handling gas systems to maintain high safety awareness.
Emergency Procedures
In the event of an emergency, having established procedures is crucial:
- Evacuate personnel from hazardous areas immediately.
- Shut off gas supply if safe to do so.
- Report the incident to safety personnel and prepare for necessary medical attention if injuries occur.
- Conduct a full review of the incident post-emergency to improve future safety protocols.
Advanced Features in Nitrogen Regulators
Smart Technology Integration
Modern nitrogen regulators are increasingly incorporating advanced technology for improved monitoring and control:
- Digital Gauges: Offer precise readings and real-time data that can be logged and analyzed over time.
- Automated Shutoff: Some regulators come equipped with automated shutoff features that activate when predetermined pressure levels are reached.
- Connectivity: Some advanced systems allow for remote monitoring and control via smartphones or computer applications, enhancing user convenience.
Dual and Single Outlet Options
Choosing between single and dual outlet regulators depends on the complexity of the application:
- Single Outlet Regulators: Suitable for simple applications where one source of nitrogen is needed.
- Dual Outlet Regulators: These allow users to maintain multiple connections with different pressure settings, useful in complex systems.
The Future of Nitrogen Regulator Technology
As industries evolve, so too does nitrogen regulator technology. Some trends shaping the future of these devices include:
- Increased automation to reduce the risk of human error.
- Enhanced data analytics capabilities to provide insights into usage patterns and efficiency.
- Robust safety features that integrate smart technology to alert users of potential hazards.