Top Blow Molding Machine Manufacturer: Enhancing Production Efficiency and Quality
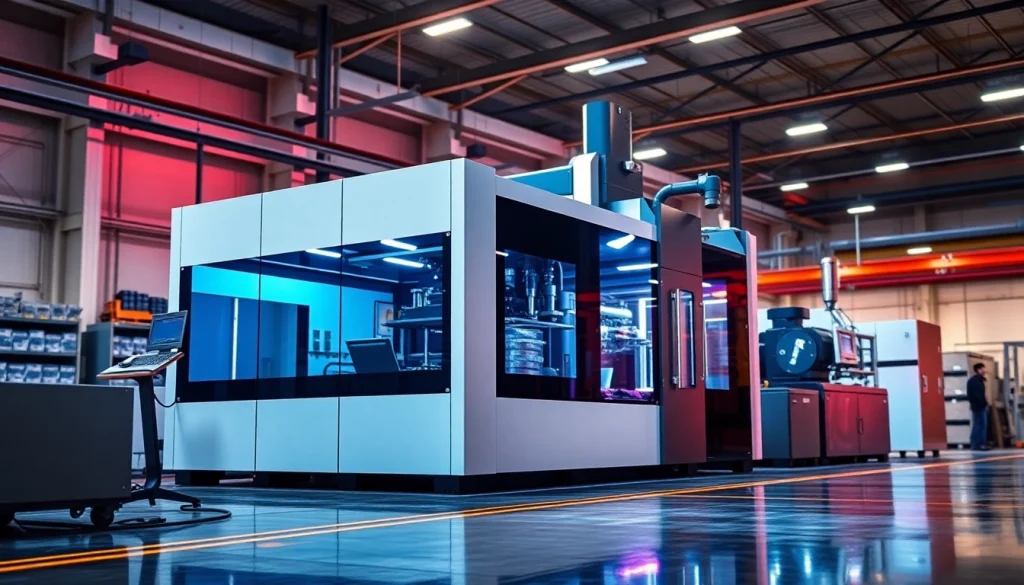
Understanding Blow Molding Technology
The Basics of Blow Molding
Blow molding is a highly efficient process used in the manufacturing of hollow plastic objects such as bottles, containers, and tanks. The fundamental working principle involves the creation of a parison (a hollow tube of plastic) which is then inflated under pressure into a preformed mold. This method not only allows for the rapid production of plastic parts but also ensures a high level of uniformity and quality of the finished products.
Types of Blow Molding Processes
There are primarily three types of blow molding processes:
- Extrusion Blow Molding (EBM): This process involves extruding a tube of molten plastic, which is then captured in a mold and inflated. It’s commonly used for producing larger parts.
- Injection Blow Molding (IBM): In this method, the parison is created inside a mold via injection molding, followed by the blowing of the mold to form the final object. This technique is ideal for creating small, precise parts.
- Stretch Blow Molding (SBM): This process not only stretches the parison but also enhances the strength of the final product. SBM is particularly popular in the production of PET bottles due to its ability to produce high clarity and strength.
Applications in Various Industries
Blow molding is integral in a wide array of industries. The packaging industry, particularly beverage production, is one of the largest consumers of blow-molded products. Beyond consumer goods, sectors such as automotive, medical, and industrial applications also utilize blow molding for creating specific components that require lightweight and durable materials.
Why Choose a Reliable Blow Molding Machine Manufacturer
Key Factors in Selecting a Manufacturer
When selecting a blow molding machine manufacturer, several critical factors come into play. You should consider the following:
- Machine Versatility: A manufacturer offering a variety of machine models should fit diverse production needs.
- Technological Innovations: Emphasis on recent technological advancements can indicate a manufacturer’s commitment to quality and efficiency.
- Customization Options: The ability to customize machines according to specific production requirements is invaluable.
Reputation and Client Feedback
Reputation is a fundamental aspect of choosing a blow molding machine manufacturer. Prospective buyers should seek feedback from existing clients, examine case studies, and read reviews extensively. Established manufacturers often have a track record reflected in their longevity in the market and customer loyalty. For instance, Uniloy is recognized as a global leader in blow molding technologies, noted for offering diverse systems tailored to specific production needs.
Post-Purchase Support and Maintenance
The journey with a blow molding machine does not end after the purchase. Reliable manufacturers provide continuous support, including training for staff, spare parts provision, and regular maintenance services. Evaluating the responsiveness and expertise of the post-purchase support is crucial in ensuring long-term operational efficiency.
Innovations and Trends in Blow Molding Machines
Emerging Technologies in Blow Molding
Innovation is at the core of blow molding technology, with numerous advancements enhancing product quality and production efficiency. Notable innovations include:
- High-Speed Machines: Newer machines can produce bottles at significantly higher rates, meeting market demands more effectively.
- Smart Sensors and Automation: Incorporating smart technology to monitor machine performance and automate processes enhances productivity and reduces human error.
Sustainability in Machine Design
With increasing awareness of environmental concerns, sustainability is becoming a pivotal factor in machine design. Modern blow molding machines are now being designed to minimize material waste, consume less energy, and utilize recyclable materials. Manufacturers committing to sustainable practices are appealing to eco-conscious brands and organizations.
Industry 4.0 Integration
The integration of Industry 4.0 technologies has revolutionized the blow molding landscape. This includes advanced data analytics, IoT capabilities, and cloud computing, allowing manufacturers to track production metrics in real-time. Such integration facilitates predictive maintenance, optimizing the operational lifespan of machines and reducing downtime.
Case Studies of Successful Implementations
Manufacturer A: Case Study of High-Speed Production
This case study explores Manufacturer A’s investment in a cutting-edge blow molding machine that increased their production capacity by 50%. By implementing high-speed technology, they were able to cater to rising consumer demands while maintaining product quality, demonstrating the importance of technology in competitive markets.
Manufacturer B: Sustainable Practices in Blow Molding
Manufacturer B integrated sustainable practices by investing in energy-efficient blow molding machines and using post-consumer recycled plastics in their processes. This strategic pivot not only decreased their operational costs but also significantly enhanced their brand image and market appeal.
Manufacturer C: International Expansion and Technology Adoption
With a focus on international growth, Manufacturer C adopted new blow molding technologies and expanded their operational reach into emerging markets. This expansion was facilitated by partnering with a reliable Blow Molding Machine Manufacturer, ensuring that they had the latest technology to meet the diverse needs of new markets.
Getting Started with Your Blow Molding Machine
Initial Inquiries and Setup Considerations
Before purchasing a blow molding machine, initial inquiries should revolve around your production needs and facility capabilities. Consider factors such as space availability, required production volume, and desired machine capabilities. Manufacturers often provide consultations to align equipment characteristics with operational goals.
Training Your Staff for Optimal Operations
Effective training is vital for operating blow molding machines efficiently. A well-trained workforce can reduce errors, enhance productivity, and ensure safety protocols are followed. Manufacturers frequently provide comprehensive training programs, including operator manuals, online courses, and hands-on workshops.
Measuring Performance and ROI
After implementation, measuring the performance of your blow molding machine is crucial for assessing its impact on production. Key performance indicators (KPIs) such as production output, defect rates, and energy consumption provide insights into operational efficiency. Additionally, tracking the return on investment (ROI) will help justify the initial expenditure and guide future investments in technology.