Leading Blow Molding Machine Manufacturer Delivering Innovative Solutions for Manufacturing Efficiency
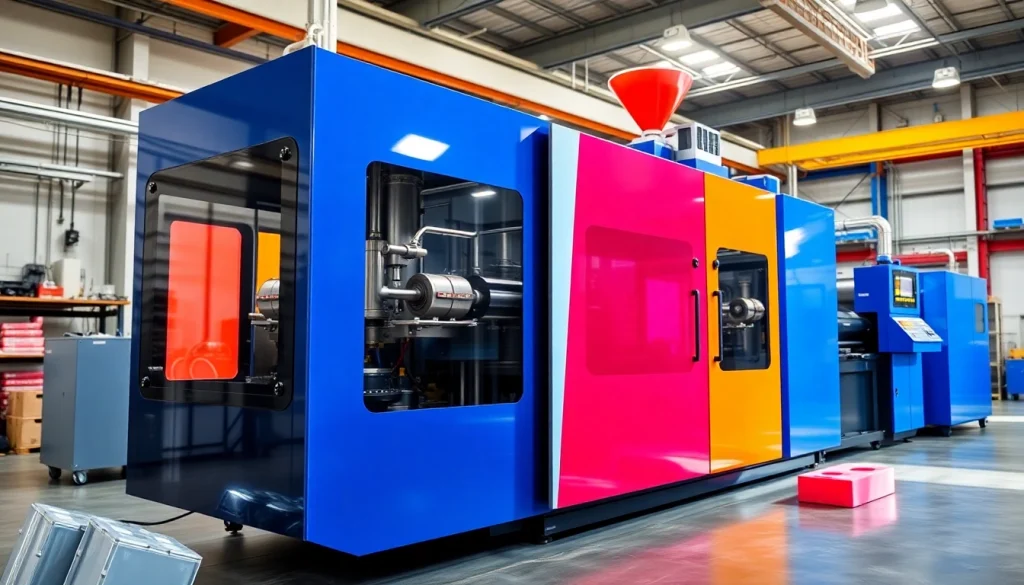
Understanding Blow Molding Technology
Blow molding is a vital manufacturing process for producing hollow plastic parts. It encompasses various technologies that are widely used across industries, from packaging to automotive. Understanding the blow molding technology is crucial for manufacturers aiming for efficiency and innovation in production. The role of a competent Blow Molding Machine Manufacturer is key in this landscape.
What is Blow Molding?
Blow molding is a manufacturing process that creates hollow plastic parts by inflating a heated plastic tube until it fills a mold. The process can streamline production compared to traditional methods, making it a popular choice in the plastic industry. The procedure typically consists of three main phases: the formation of a parison, inflation, and cooling. Understanding these phases allows manufacturers to fine-tune their operations for better quality and efficiency.
Types of Blow Molding Processes
There are several types of blow molding processes that manufacturers can adopt, each with its unique applications and benefits:
- Extrusion Blow Molding (EBM): This method involves extruding a parison and using air pressure to inflate it into a mold. It’s commonly used for items like bottles, containers, and tanks.
- Injection Blow Molding (IBM): This combines injection molding and blow molding to create complex shapes with greater precision. It is best used for small to medium-sized containers.
- Stretch Blow Molding: This method stretches the parison before inflation, which enhances the material’s orientation, making the final product stronger and lighter.
- Reheat Stretch Blow Molding (RSBM): Suitable for PET bottles, this process initially produces a preform, which is later reheated and stretched into shape.
Applications of Blow Molding Technology
The versatility of blow molding technology extends into various sectors:
- Packaging: Blow molding is extensively used in the production of bottles, jars, and containers, primarily for food and beverage industries.
- Automotive: Utilizing blow molding for manufacturing automotive parts, like fuel tanks and air ducts, reduces weight while maintaining strength.
- Consumer Products: Household items such as toys, sporting goods, and appliances often employ blow molding technology for efficient production.
- Medical Devices: With the precision that blow molding can achieve, manufacturers produce items like syringes and medical containers.
Choosing the Right Blow Molding Machine
Selecting the right blow molding machine is critical for meeting production demands and achieving operational efficiency. Factors such as machine type, manufacturer reputation, and technology specifics play significant roles in this decision-making process.
Factors to Consider When Selecting a Manufacturer
When engaging with a blow molding machine manufacturer, consider:
- Experience and Expertise: Look for manufacturers with proven success and industry experience.
- Technology Offerings: Evaluate the range of technologies available—such as EBM, IBM, and stretch molding—to meet your production needs.
- Customer Support: After-sales service and technical support can make a significant difference in equipment longevity and efficiency.
- Cultural Fit: The manufacturer’s values and business practices should align with your company’s ethos.
Key Features of Modern Blow Molding Machines
Modern blow molding machines come equipped with various features designed to enhance productivity and minimize waste:
- Automated Control Systems: Advanced controls allow for precise adjustments during the molding process, enhancing consistency while reducing material waste.
- Energy Efficiency: Look for machines with low energy consumption rates without compromising production capabilities.
- Multilayer Capabilities: Certain systems can produce multilayer structures, allowing for better barrier properties in packaging.
- Remote Monitoring: Some machines now offer IoT capabilities, allowing manufacturers to monitor and manage operations remotely, thus increasing uptime.
Cost Considerations in Purchasing
When purchasing a blow molding machine, consider the total cost of ownership rather than just the initial investment:
- Initial Investment: Compare prices among various manufacturers but focus on long-term returns.
- Operating Costs: Evaluate operational efficiencies, including power consumption, maintenance, and downtime.
- Training and Support Costs: Factor in the cost of training staff and the potential need for ongoing technical support.
- Opportunity Costs: Consider how the machine’s capabilities align with your growth strategies.
Top Blow Molding Machine Manufacturers
The blow molding industry features several prominent manufacturers, each offering unique strengths and technologies.
Profiles of Leading Companies in the Industry
Some of the foremost blow molding machine manufacturers include:
- Uniloy: Known for innovative designs and an extensive selection of blow molding technologies, Uniloy has established itself as a global leader.
- Wilmington Machinery: Renowned for high-speed, multilayer blow molding machines, they cater to industries requiring efficient, high-quality production.
- Jomar Corporation: With half a century in injection blow molding, Jomar specializes in customized solutions for specific market needs.
- Bekum Maschinenfabrik: They lead the way with sophisticated dual-station machines, catering to the American market with efficiency-driven designs.
Comparing Technologies and Offerings
Each blow molding technology provides distinct advantages, and manufacturers must assess which best fits their operational needs:
- Market Reach: Understand how different technologies impact the ability to penetrate new markets or industries.
- Product Versatility: Compare how diverse products can be manufactured using each technology; this flexibility may counterbalance initial cost differences.
- Quality and Consistency: Evaluate historical performance metrics and customer reviews to make informed comparisons.
Market Trends and Innovations
The blow molding industry is evolving with new innovations, including:
- Biodegradable Materials: Growing consideration for sustainability is leading manufacturers to explore biodegradable and eco-friendly materials.
- Smart Manufacturing: The integration of smart technology, including AI and predictive analytics, is transforming operational efficiencies and product quality.
- Customization: Increased demand for custom and specialized designs requires manufacturers to adopt more agile production methods.
Maintaining Your Blow Molding Equipment
Efficient maintenance is vital for the longevity and performance of blow molding machinery. A proactive approach enables manufacturers to mitigate breakdowns and extend equipment life.
Best Practices for Upkeep and Longevity
To ensure optimal machine performance, consider the following maintenance practices:
- Regular Inspections: Establish a schedule for routine inspections to detect and address potential issues early.
- Lubrication: Keep moving parts well-lubricated and replace worn components as needed.
- Cleanliness: Maintaining a clean workspace and machine environment can prevent contaminants from affecting production.
- Training Personnel: Ensure operators are well-trained in machine operation and maintenance protocols.
Common Issues and Troubleshooting
Manufacturers often encounter issues that can disrupt production. Here are some common problems and potential troubleshooting solutions:
- Inconsistent Wall Thickness: Check for uniform heating and ensure proper parison dimensions to avoid this issue.
- Dimensional Variability: Investigate machine calibrations and mold precision to enhance the consistency of product dimensions.
- Frequent Downtime: Analyze production patterns to identify specific causes of downtime, from machine malfunctions to supply chain issues.
Service and Support Options
Partnering with a reputable blow molding machine manufacturer ensures access to essential servicing and support:
- Technical Support: Assess the availability of technical assistance from the manufacturer, especially during critical production phases.
- Spare Parts Availability: Ensure that spare parts are readily accessible to minimize downtime in case of breakage.
- Upgrade Guidelines: Manufacturers should provide clear pathways for equipment upgrades, ensuring that clients can adapt to changing market needs.
Future of Blow Molding Machinery
As industries evolve, so too must the technologies that support them. The future of blow molding machinery will be shaped by several critical trends and advancements.
Advancements in Technology
Emerging advancements are expected to drastically enhance the capabilities of blow molding machines. These include:
- AI and Machine Learning: Utilizing AI for predictive maintenance and operational efficiency can significantly cut costs and prolong machine lifespan.
- Advanced Robotics: Integration of robotics may streamline the material handling processes, thus speeding up production cycles and reducing labor costs.
- IoT Connectivity: Enhanced connectivity allows for real-time monitoring and optimization of production workflows, improving overall efficiency.
Environmental Considerations and Sustainability
Manufacturers are increasingly guided by environmental regulations and consumer preferences for sustainable practices:
- Recyclable Strategies: Emphasis on developing recyclable and low-impact materials will continue to grow.
- Energy Efficiency: Government incentives for energy-efficient machinery encourage manufacturers to invest in sustainable technologies.
- Life Cycle Assessments: Companies are increasingly adopting life cycle assessments to evaluate their environmental impacts and improve sustainability.
Preparing for Industry Changes and Expectations
As the blow molding market continues to evolve, manufacturers must prepare for forthcoming changes:
- Market Demand Shifts: Stay ahead of consumer trends in packaging and consumer goods to remain competitive.
- Technological Adoption: Embrace advancements in technology and stay adaptable to keep pace with the industry.
- Training and Upskilling Workforce: Ensure that employees continuously gain skills in emerging technologies for effective adoption.