Essential Guide to Choosing the Right Clamp on Hose for Your Needs
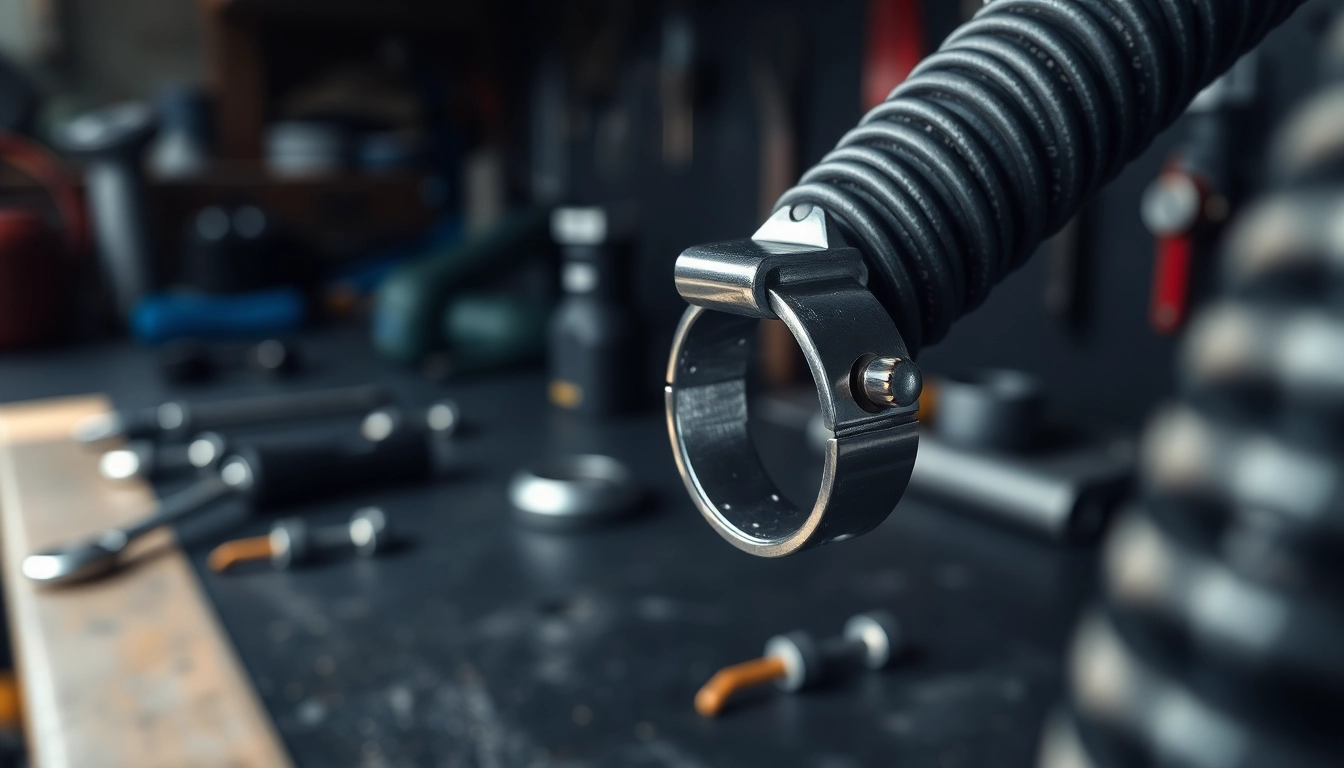
Understanding Clamp on Hose Basics
Clamp on hoses are essential components in a variety of applications, ranging from automotive to industrial uses. Their primary function is to secure hoses in place, preventing leaks and ensuring efficient fluid transfer. The increasing demand for reliable clamp on hose solutions has led to a diverse array of products on the market. This guide aims to unravel the intricacies of clamp on hoses, helping you make informed decisions based on your specific needs.
What is a Clamp on Hose?
A clamp on hose is a type of flexible tubing that is attached to a connection point using a hose clamp. The clamp provides a secure seal to prevent fluid leaks and is crucial for maintaining integrity in systems that convey liquids or gases. Clamp on hoses are commonly used in various settings, including automotive engines, plumbing systems, and industrial machinery.
Types of Clamp on Hoses
There are several types of clamp on hoses, and choosing the right type is crucial depending on the application:
- Worm Gear Clamps: These are made of stainless steel and feature a screw mechanism for adjustable tension. They are widely used due to their versatility.
- Spring Clamps: Designed for quick applications, spring clamps are often used in automotive and industrial settings where rapid connection and disconnection are needed.
- T-Bolt Clamps: Known for providing a robust seal, T-bolt clamps are ideal for high-pressure applications and heavy-duty machinery.
- Hose Pinch Clamps: Commonly used in plumbing, these clamps provide a simple yet effective means to seal hoses without the need for tools.
Applications of Clamp on Hose in Various Industries
Clamp on hoses see extensive use across multiple industries:
- Aerospace: In aerospace applications, clamp on hoses are used to maintain fuel integrity and manage fluids within engines.
- Automotive: In vehicles, they play a critical role in engine cooling systems, fuel delivery, and exhaust systems.
- Manufacturing: Many manufacturing processes rely on clamp on hoses to move liquids and granules through production lines efficiently.
- HVAC Systems: Clamp on hoses are also essential in heating, ventilation, and air conditioning systems to maintain airflow and fluid transfer.
Choosing the Right Clamp on Hose
Factors to Consider When Selecting a Clamp on Hose
When selecting a clamp on hose, several factors must be considered to ensure optimal performance:
- Diameter: The internal diameter of the hose must match the fittings it will connect to for a proper seal.
- Material: Depending on the fluid type, choose a material resistant to chemicals, temperature fluctuations, and pressure changes.
- Length: Ensure the hose is adequately long enough for the application while facilitating easy manipulation.
- Pressure Rating: Review the pressure ratings to ensure the hose can withstand the operational pressures without failure.
Comparison of Materials Used in Clamp on Hoses
Clamp on hoses are made from various materials, each offering distinct advantages:
- Rubber: Flexible and resistant to wear, rubber hoses are ideal for general applications and moderate pressure levels.
- PTFE (Teflon): Known for its chemical resistance, PTFE hoses are suitable for harsh environments and high temperatures.
- Silicone: Flexible and durable, silicone hoses maintain performance across a wide temperature range, making them suitable for automotive and industrial uses.
- Metal: Metal hoses provide excellent pressure handling and temperature resistance, commonly used in severe-duty conditions.
Common Mistakes to Avoid When Choosing Your Clamp on Hose
Choosing the wrong clamp on hose can lead to failures, leaks, or safety hazards. Here are common pitfalls to avoid:
- Using a hose with an incorrect diameter can lead to leaks or disconnections.
- Neglecting to consider the operating environment may result in hose degradation.
- Overlooking the importance of pressure ratings can compromise system safety.
- Choosing the cheapest option without considering material quality may prove costly in the long run.
Installation Tips for Clamp on Hose
Step-by-Step Guide to Installing a Clamp on Hose
Installing a clamp on hose correctly is essential for ensuring optimal performance:
- Measure and cut the hose to the required length.
- Ensure both ends of the hose are clean and free from debris.
- Position the hose over the fitting firmly.
- Place the clamp around the hose and fitting.
- Tighten the clamp securely using the appropriate tool (typically a screwdriver).
- Inspect the connection for any signs of leakage or improper fitting.
- Test the system under operational conditions to confirm stability.
Tools Required for Installation
To install a clamp on hose efficiently, you may need the following tools:
- Measuring tape for precise length measurement.
- Cutting tool for trimming the hose to size.
- Screwdriver or wrench for tightening the clamps.
- Inspection mirror for hard-to-see connections.
- Safety glasses to protect against debris during installation.
Best Practices for Securing Clamp on Hose
To ensure longevity and reliability of clamp on hose installations, follow these best practices:
- Always respect the manufacturer specifications for tightening torque.
- Regularly inspect clamps for signs of wear or loosening.
- Use compatible hose materials and clamps to prevent connection failures.
- Apply lubricant to threaded clamps to facilitate easier adjustments.
Maintenance of Clamp on Hose
How to Inspect Your Clamp on Hose Regularly
Regular inspections can help identify potential issues before they lead to failures. Key inspection points include:
- Visual checks for cracks, bulges, or wear on the hose.
- Ensuring clamps remain secure and tight, with no sign of slipping.
- Listening for unusual noises that may imply fluid or gas leakage.
Signs of Wear and When to Replace
Knowing when to replace a clamp on hose is crucial for maintaining system integrity. Key signs include:
- Visible cracks or split seams along the hose.
- Frequent leaks at connection points, despite adjustment.
- Discoloration or hardening of the material.
- Loss of flexibility, indicating material fatigue.
Cleaning Techniques for Long-lasting Performance
To maintain clamp on hoses in optimal condition, consider employing these cleaning techniques:
- Utilize a mild detergent and water solution for surface cleaning.
- For stubborn residue, consider using a soft brush to avoid scratching the hose surface.
- Ensure the hose is thoroughly dried before use to prevent mold or mildew buildup.
Performance Metrics for Clamp on Hose
Evaluating the Efficiency of Your Clamp on Hose
To assess the efficiency and effectiveness of your clamp on hose, consider monitoring the following metrics:
- Fluid flow rate, ensuring it meets operational requirements.
- Pressure drops across the hose during operation.
- Frequency of maintenance checks and associated findings.
- Cost of repairs or replacements over time, weighing it against operational efficiency.
Case Studies: Successful Applications of Clamp on Hose
Real-world case studies demonstrate the application of effective hose clamping solutions:
Case Study 1: A manufacturing plant replaced rubber hoses with PTFE options, resulting in a 15% decrease in fluid transfer losses due to enhanced pressure capabilities.
Case Study 2: In a maritime application, T-bolt clamps secured hoses against high-pressure seawater, leading to zero leaks throughout the season and reducing downtime significantly.
Customer Feedback: Real-World Experiences with Clamp on Hose
Customer experiences yield insight into the effectiveness of specific clamp on hose solutions:
One automotive technician noted significant improvement in engine performance after switching to stainless steel worm gear clamps, highlighting their reliability under high-temperature conditions.
Another user in the chemical industry praised the chemical resistance of PTFE hoses, emphasizing reduced maintenance costs and improved safety on their production floors.