Precision Die Cutting: The Key to Custom Manufacturing Solutions
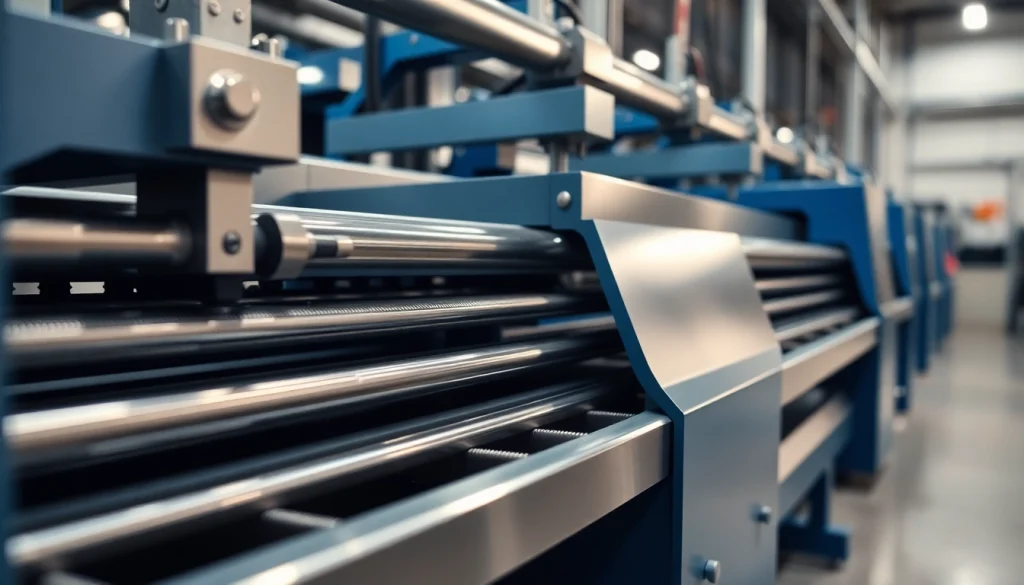
Understanding Precision Die Cutting
In the realm of modern manufacturing, precision die cutting stands out as a critical process for producing custom shapes with exceptional accuracy. This technique allows manufacturers to transform raw materials into precisely cut parts and components that meet specific design requirements. With its ability to handle various materials and deliver high-quality results, precision die cutting has become an essential service for industries ranging from automotive to healthcare.
What is Precision Die Cutting?
Precision die cutting is a manufacturing process that utilizes a die to cut materials into specified shapes and sizes with high accuracy. The die can be made from various materials, including steel, and functions by stamping or cutting shapes from sheets or rolls of materials such as paper, plastics, rubber, metals, and fabrics. This method is particularly effective for producing large quantities of uniform parts quickly and cost-effectively.
The two primary types of die cutting are flatbed die cutting and rotary die cutting. Flatbed die cutting employs a stationary flatbed onto which the material is placed, and a die is pressed down to cut the material. In contrast, rotary die cutting utilizes a cylindrical die to cut materials as they pass through a machine, enabling higher speeds for mass production.
Benefits of Precision Die Cutting for Industries
Precision die cutting offers a plethora of benefits that make it an attractive option for various sectors:
- High Accuracy: The ability to produce parts with tight tolerances within +/- 0.005 inches enhances the quality of the final products, crucial for applications in electronics and medical devices.
- Efficiency: Automated die cutting processes enable rapid production speeds, allowing companies to meet high-volume demands without sacrificing quality.
- Versatility: This process can accommodate a wide range of materials and can create intricate shapes and designs, making it suitable for diverse applications.
- Cost-effective: For large runs of products, precision die cutting reduces waste and lowers per-unit costs, providing a significant economic advantage.
Common Applications of Precision Die Cutting
The applications of precision die cutting are vast and varied. Some of the most common include:
- Automotive Industry: Components such as gaskets, seals, and insulation materials are commonly produced using precision die cutting to ensure they meet stringent quality and performance standards.
- Medical Devices: Intricate parts used in diagnostic equipment, surgical instruments, and medical packaging benefit from the accuracy and reliability of precision die cutting.
- Consumer Products: Items like labels, packaging, and custom promotional materials are often created with this technique, enhancing brand identity and marketing efforts.
- Electronics: Precision-cut parts for electronic devices, including insulation, EMI/RFI shielding, and functional components, ensure both usability and safety in electronic applications.
Types of Precision Die Cutting Techniques
Straight Cutting vs. Rotary Die Cutting
Straight cutting and rotary die cutting are the two primary techniques employed in precision die cutting, each serving different needs:
Straight Cutting
Straight die cutting, often associated with flatbed presses, involves a single die press cutting through the material from above. This method is particularly beneficial for larger parts, intricate designs, and when using thicker materials. While it typically has a longer setup time and lower speed, it is highly effective for smaller production runs.
Rotary Die Cutting
In contrast, rotary die cutting offers high-speed production through a rotary die mechanism. This technique is ideal for continuous web materials, reducing waste and allowing for fast, repetitive processing. It’s especially advantageous for products requiring high volumes, such as adhesive labels, cartons, and flexible packaging.
Laser Cutting: A Modern Approach
With advancements in technology, laser cutting has emerged as another pivotal method in precision die cutting. Utilizing a high-powered laser, this technique offers unparalleled accuracy for intricate designs. The benefits of laser cutting include:
- Precision: Laser cutting can achieve incredibly tight tolerances, often within +/- 0.001 inches.
- No Tool Wear: As lasers do not physically touch the material, wear and tear on cutting implements are minimized, leading to consistent precision over long production runs.
- Material Flexibility: It can cut a variety of materials, including metals, wood, acrylics, and composites, making it highly versatile.
Choosing the Right Technique for Your Needs
Selecting the appropriate die cutting technique depends on several factors, including:
- Material Type: Evaluate the nature and thickness of the material to determine if straight cutting or rotary cutting is more suitable.
- Production Volume: For high-volume production, rotary die cutting is typically more efficient, while lower volumes might benefit from straight cutting.
- Cost Considerations: Analyze the costs involved in each cutting type, including setup and production, to determine the most economical option for the project.
Factors Influencing Precision in Die Cutting
Material Selection for Optimal Results
The success of precision die cutting hinges significantly on the selection of the right materials. Factors to consider include:
- Material Thickness: Different materials exhibit varying levels of cutting difficulty; knowing the thickness is crucial for selecting the right cutting method.
- Material Composition: The inherent properties of the material, such as flexibility and density, affect the precision cutting ability and should guide the choice of techniques.
- Surface Treatment: Surface finishes can influence adhesion, cutting ease, and final product quality, making it vital to factor these in during the material selection phase.
Machine Calibration and Maintenance
To maintain precision in die cutting, proper machine calibration and maintenance are essential. Regular inspections and servicing help prevent inaccurate cuts and extend the lifespan of the equipment. Key practices include:
- Routine Checks: Regularly inspect machines for alignment and wear and tear on dies to ensure consistent performance.
- Software Updates: Keeping control software up to date improves precision and efficiency, particularly for laser cutting systems.
- Operator Training: Investing in operator training can significantly impact production quality, as skilled operators are better equipped to handle machine adjustments.
Tolerances: Achieving Accurate Dimensions
Achieving the desired tolerances is crucial for the precision die cutting process. Typical tolerances can vary depending on the type of die cutting method used. For instance:
- Steel rule dies may allow tolerances from +/- 0.005 inches to +/- 0.15 inches, depending on design complexity.
- Rotary die cutting usually achieves tighter tolerances than straight cutting, making it suitable for applications demanding high precision.
Creating a detailed specifications document before the production stage is crucial to align expectations between manufacturers and clients regarding tolerances.
Measuring Performance and Quality
Key Performance Indicators for Die Cutting
Measuring the performance of precision die cutting involves several key performance indicators (KPIs). These include:
- Production Efficiency: Analyzing the output rate in terms of parts produced per hour helps assess the efficiency of the die cutting process.
- Quality Rate: Monitoring the percentage of parts meeting quality standards assists in identifying production issues early and facilitates continuous improvement.
- Cost per Part: Calculating the total operational costs divided by the number of parts produced provides insights into cost-effectiveness and can inform decisions on process optimizations.
Quality Control Processes in Precision Die Cutting
To ensure high-quality products, companies implement several quality control measures throughout the precision die cutting process, including:
- In-process Inspections: Regular inspections during the cutting process help catch defects before they escalate into larger issues.
- Final Product Checks: Implementing stringent checks on final products against specifications ensures compliance with customer requirements.
- Feedback Loops: Creating feedback mechanisms allows operators to report issues and implement solutions for continuous improvement.
Customer Satisfaction Metrics and Feedback
Collecting customer feedback is vital to enhancing service quality and aligning produced parts with customer expectations. Companies often use surveys and direct feedback channels to understand client satisfaction levels, focusing on metrics such as:
- Came in on Time: Evaluating if products are delivered as per the agreed timelines.
- Parts Meet Expectations: Gathering insights on whether the final products meet the desired specifications.
- Reorder Rates: Tracking repeat orders can indicate client satisfaction and the effectiveness of the precision die cutting services provided.
Future Trends in Precision Die Cutting
Technological Advancements and Innovations
The future of precision die cutting appears promising, driven by ongoing technological advancements. Emerging trends include:
- Automation: The rise of automated die cutting systems enhances efficiency and reduces human error during production.
- Industries 4.0: Integration of internet-connected devices helps monitor production in real time, optimizing processes and resources.
- Advanced Materials: Development of new, lighter, and more durable materials will continue to expand the capabilities of precision die cutting.
Environmental Considerations and Sustainable Practices
As industries lean towards sustainability, precision die cutting is evolving with a focus on environmental practices. This includes:
- Reducing Material Waste: Implementing techniques that minimize offcuts and scraps during production.
- Energy-efficient Machines: Investing in technology that reduces energy consumption during the die cutting process.
- Recycling Initiatives: Encouraging the recycling of materials, ensuring that byproducts of cutting processes are reused or repurposed.
Market Demand and Industry Insights
With innovations and growing efficiency, the demand for precision die cutting is increasing across various sectors. Insights from industry analyses show:
- Healthcare and electronics markets are particularly influential, driving demand for accurate, custom-cut components.
- Global trends towards personalized products increase the need for high-quality, short-run die cutting solutions.
- Companies are investing in R&D to enhance precision and expand service offerings, ensuring competitiveness in a rapidly evolving market.